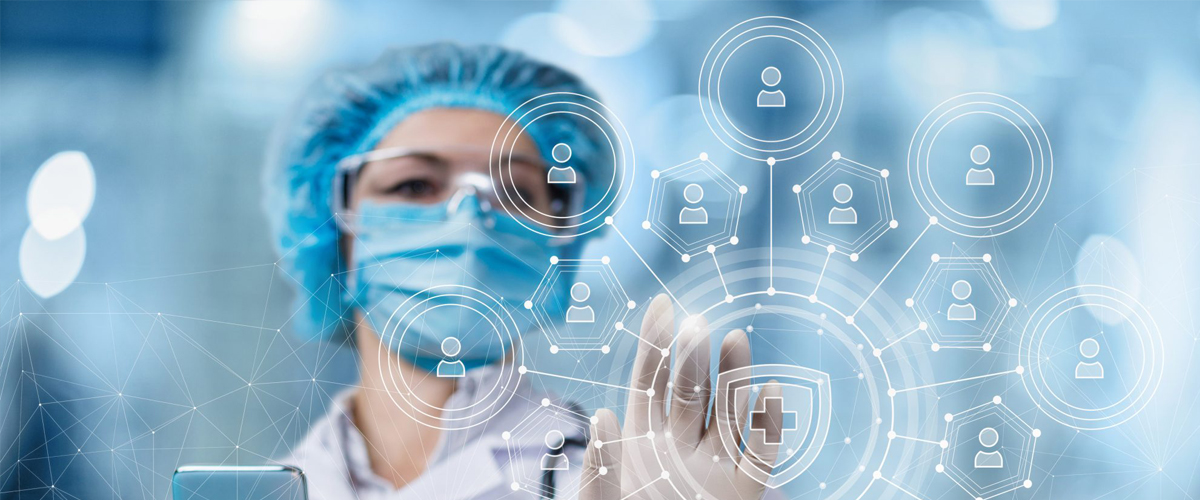
CDSCO Device Classification
ISO 13485 is an internationally recognized Quality Management System (QMS) standard tailored for the medical device industry, ensuring that organisations consistently meet both regulatory and customer requirements for safety and performance. This standard is critical for medical device testing, manufacturing, and maintaining adherence to stringent medical device standards. ISO 13485 encompasses all aspects of the product life cycle, from design and development through production, installation, and servicing, with a strong emphasis on regulatory submissions and compliance.
Fifth Schedule: ISO 13485
The Quality Management System for medical devices and in vitro diagnostic medical devices is included in the fifth schedule of The Medical Device Rules 2017.This schedule specifies requirements for a quality management system that shall be used by the manufacturer for the design and development, manufacture, packaging, labelling, testing, installation and servicing of medical devices and in vitro diagnostic medical devices. If the manufacturer does not carry out design and development activity, the same shall be recorded in the quality management system. The manufacturer shall maintain conformity with this Schedule to reflect the exclusions.
According to this schedule:
The processes required by this Schedule, which are applicable to the medical device and in-vitro diagnostic medical device, but which are not performed by the manufacturer are the responsibility of the manufacturer and are accounted for in the manufacturer’s quality management system.
If a manufacturer engages in only some operations subject to the requirements of this part, and not in others, that manufacturer need only to comply with those requirements which are applicable to the operations in which it is engaged.
It is emphasised that the quality management system requirements specified in this Schedule are in addition to complementary to technical requirements for products.
Manufacturers of components or parts of finished devices and in vitro diagnostic medical devices are encouraged to use appropriate provisions of this schedule as guidance.
The general requirements as specified by this schedule are as follows:
The manufacturer shall establish, document, implement and maintain a quality management system and maintain its effectiveness in accordance with the requirements of this schedule. The manufacturer shall: -
identify the processes needed for the quality management system and their application throughout the organisation;
determine the sequence and interaction of these processes;
determine criteria and methods needed to ensure that both the operation and control of these processes are effective;
ensure the availability of resources and information necessary to support the operation and monitoring of these processes;
monitor, measure and analyse these processes; and
implement actions necessary to achieve planned results and maintain the effectiveness of these processes.
These processes shall be managed by the manufacturer in accordance with the requirements of this Schedule. Where a manufacturer chooses to outsource any process that affects product conformity with requirements, the manufacturer shall ensure control over such processes. Control of such outsourced processes shall be identified within the quality management system.
Here at IQZYME, we help organisations navigate complex medical device regulations, including CDSCO compliance, ensuring that all regulatory submissions meet the necessary standards. The standard also integrates risk management practices, aligned with ISO 14971, to identify and mitigate risks associated with medical devices, thus ensuring patient safety. Through a process-based approach, ISO 13485 mandates rigorous documentation and control procedures, essential for maintaining a robust Quality Management System. Compliance consulting and regulatory affairs play a crucial role in implementing and maintaining ISO 13485 QMS, ensuring that organisations adhere to regulatory requirements, including those for CDSCO projects.
At IQZYME, we understand that a robust Quality Management System (QMS) is the backbone of any successful pharmaceutical or medical device company. Our QMS services are designed to help you implement and maintain a comprehensive system that ensures your products meet the highest standards of quality, safety, and compliance. With a focus on regulatory frameworks such as ISO 13485 and the Central Drugs Standard Control Organization (CDSCO) guidelines, our experts provide tailored solutions to align your processes with industry best practices.
From initial system design to ongoing audits and continuous improvement, IQZYME offers end-to-end support to ensure your QMS is efficient and effective. We assist in developing standard operating procedures (SOPs), conducting risk assessments, and training your staff to adhere to quality standards. Our goal is to help you achieve and maintain certification, ensuring that your products consistently meet regulatory requirements and exceed customer expectations. With IQZYME's QMS services, you can confidently navigate the complexities of regulatory compliance and focus on delivering high-quality products. Let us help you build a culture of quality and excellence within your organisation, ensuring that every aspect of your operations is aligned with your commitment to quality.
For medical devices, two critical factors must be addressed:
Quality Assurance: Ensuring that the medical device meets high standards of quality.
Safety: Guaranteeing that the device is safe for use.
Given the rigorous regulatory standards governing medical devices, compliance with these standards is mandatory. It is not merely about achieving basic quality metrics; organisations must demonstrate their ability to manage and uphold the quality of their medical devices comprehensively. This commitment is validated through the ISO 13485:2016 certification.
A robust quality management system is essential for the operations of a medical device manufacturer, providing a structured framework for all activities and processes. It ensures that both internal procedures and external regulations are meticulously observed and adhered to.
Securing appropriate certification not only reinforces a manufacturer's commitment to safety and quality but also builds trust in its processes and products, demonstrating a steadfast dedication to excellence and regulatory compliance.
Benefits of ISO 13485:2016 Certification
Improves company’s credibility and identity
Evidence-based decision making
Continual improvement in product process and quality
Increased employee involvement.
Enhanced customer satisfaction.
Why is ISO 13485 Certification Important?
ISO 13485 certification is crucial as it demonstrates a company's commitment to maintaining high standards of quality and regulatory compliance in the production of medical devices. It helps organisations ensure that their products are safe, effective, and meet the stringent requirements of the medical device industry.
What is the Scope of ISO 13485 Certification?
The scope of ISO 13485 certification encompasses all aspects of a medical device company's operations, including:
Design and Development: Ensuring that medical devices are designed and developed with quality and safety in mind.
Production and Manufacturing: Implementing controls and procedures to maintain high standards of production and manufacturing.
Quality Management Systems (QMS): Establishing and maintaining a robust QMS that complies with international standards and regulatory requirements.
Installation and Servicing: Ensuring that devices are properly installed and serviced, maintaining their effectiveness and safety throughout their lifecycle.
Regulatory Compliance: Adhering to local and international regulations governing medical devices.
How Can I Obtain ISO 13485 Certification in India?
To obtain ISO 13485 certification in India, follow these steps:
Implement a Quality Management System (QMS): Develop and integrate a QMS that meets the ISO 13485 requirements.
Conduct Internal Audits: Regularly review and audit your QMS to ensure compliance and identify areas for improvement.
Engage a Certification Body: Select an accredited certification body to conduct an external audit of your QMS.
Undergo Certification Audit: The certification body will perform a comprehensive audit of your QMS to assess compliance with ISO 13485 standards.
Receive Certification: Upon successful completion of the audit, you will be awarded ISO 13485 certification.