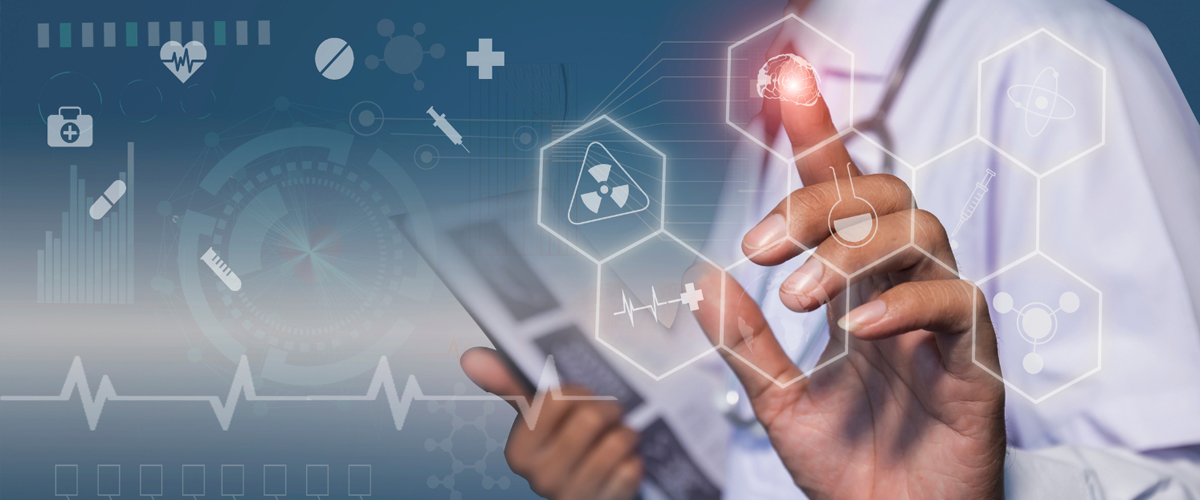
Facility Requirements
Designing a Manufacturing Plant Layout for Medical Devices is a critical first step in establishing a production facility tailored for medical device manufacturing. These requirements include stringent guidelines on clean room classifications, ISO standards, environmental controls, and other key aspects of the facility's infrastructure.
Clean Room Facility Requirements and ISO Classification
Ensuring Optimal Conditions for Medical Device Manufacturing
Clean rooms are critical environments for manufacturing medical devices, ensuring that products meet stringent quality and safety standards. These controlled environments are essential for preventing contamination and maintaining the integrity of sensitive processes. IQzyme provides expert guidance on designing and maintaining clean rooms that comply with ISO classifications, supporting your commitment to quality and regulatory compliance.
Our Clean Room and ISO Classification Services
Facility Design and Planning
Customised Design Solutions: Develop tailored clean room designs that meet your specific manufacturing needs, ensuring efficient workflow and contamination control.
Space Utilisation: Optimise space utilisation to accommodate equipment, personnel, and processes while maintaining compliance with clean room standards.
ISO Classification Compliance
ISO 14644 Standards: Ensure compliance with ISO 14644 standards, which define the classification of air cleanliness and specify the maximum allowable particle concentrations.
Classifications and Requirements: Assist in selecting the appropriate ISO classification for your clean room, such as ISO Class 5, 6, 7, or 8, based on your product and process requirements.
HVAC and Air Filtration Systems
System Design: Design HVAC and air filtration systems to maintain the required temperature, humidity, and particulate levels in your clean room.
Airflow Management: Implement airflow management strategies, including laminar and turbulent flow, to prevent contamination and ensure a clean environment.
Monitoring and Validation
Environmental Monitoring: Establish and implement environmental monitoring programs to continuously assess air quality, temperature, humidity, and other critical parameters.
Validation and Certification: Conduct validation and certification of your clean room facilities to demonstrate compliance with regulatory standards and ISO classifications.
Operational Support and Training
Standard Operating Procedures (SOPs): Develop SOPs for clean room operation, maintenance, and personnel protocols to ensure consistent compliance and quality.
Training Programs: Provide training for personnel on clean room best practices, including gowning procedures, contamination control, and environmental monitoring.
Clean Room Requirements
Clean rooms are meticulously controlled environments designed to maintain specific levels of airborne particles. In medical device manufacturing, clean rooms are crucial for preventing contamination that could jeopardise product safety and efficacy. Regulatory bodies like CDSCO require that the design, construction, and operation of clean rooms adhere to stringent standards, ensuring that conditions such as temperature, humidity, and particle count are consistently maintained within prescribed limits. Continuous monitoring of the clean room environment is essential to ensure ongoing compliance with these strict standards.
To meet stringent regulatory standards, clean rooms for medical devices must adhere to specific requirements ensuring a controlled and contamination-free environment. Here’s a breakdown:
Air Quality: Essential for contamination control, clean rooms must utilise high-efficiency particulate air (HEPA) filters, capable of removing particles as small as 0.3 microns. The air must be continuously circulated and filtered to maintain positive pressure, which prevents external contaminants from entering the clean room.
Temperature and Humidity Control: Strict control over temperature and humidity is vital to inhibit microbial growth and ensure product integrity. Typically, the temperature is maintained between 18°C to 26°C (64°F to 78°F), while relative humidity is kept within 30% to 70%.
Clean Room Gowning: Personnel entering the clean room must don cleanroom-specific garments, including gowns, gloves, and head covers, to prevent the introduction of external contaminants.
Clean Room Layout: The design must minimise cross-contamination. This includes distinct zones for material and equipment storage, growing and de-gowning, and waste disposal areas.
Surface Cleanliness: All surfaces within the clean room must be smooth, easy to clean, and disinfect. They should be free of cracks, crevices, and rough edges that could harbour contaminants.
Sterilisation: A designated sterilisation area is crucial to prevent contamination of medical devices, ensuring they are sterile before use.
Monitoring and Testing: Continuous monitoring of air quality, temperature, humidity, and microbial presence is required to ensure compliance with clean room standards. Regular testing and documentation help maintain the integrity of the clean room environment.
These measures are crucial for meeting the regulatory requirements of agencies such as the FDA, CDSCO, and EU MDR, ensuring that the medical devices produced are safe and effective.
Why Choose IQzyme for Clean Room Facility Design?
Industry Expertise: Our team has extensive experience in designing and implementing clean room facilities that meet the highest standards of quality and compliance.
Tailored Solutions: We offer customised\ design and implementation services that align with your specific manufacturing processes and regulatory requirements.
Comprehensive Support: From initial planning to ongoing maintenance, we provide end-to-end support to ensure your clean room facilities meet ISO classifications and regulatory standards.
Commitment to Quality: We are dedicated to helping you maintain optimal manufacturing conditions and achieve regulatory compliance through state-of-the-art clean room facilities.