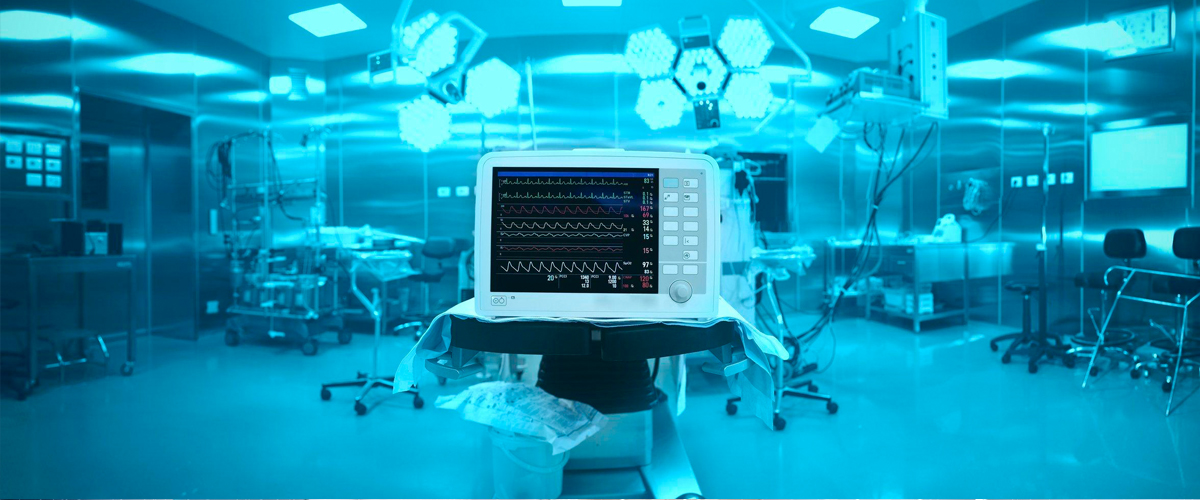
Medical Device/ivd Testing
Medical device testing is a critical process that ensures the safety, efficacy, and reliability of devices intended for patient use. This comprehensive evaluation involves several stages, including design verification, validation, and regulatory compliance testing. The process begins with rigorous testing of materials to confirm they meet biocompatibility standards and do not pose risks such as toxicity or irritation. Functional testing follows, where devices are assessed for performance under expected conditions of use, including durability, accuracy, and safety. Clinical trials may be conducted to evaluate the device's effectiveness in real-world scenarios and gather data on potential side effects. Additionally, testing often includes sterilisation validation to ensure the device is free from harmful microorganisms. This thorough testing process is crucial for gaining regulatory approvals and providing healthcare professionals and patients with reliable, effective medical technologies.
There are a number of tests involved with medical devices and IVDs for the evaluation of their safety and efficacy. Some of them are:
Biocompatibility Testing
Biocompatibility testing for medical devices is a critical evaluation process that determines whether a device is safe for contact with the human body. It assesses how materials used in the device interact with biological tissues and fluids, ensuring that the device does not cause any adverse reactions such as toxicity, irritation, inflammation, or sensitization. This testing is crucial for devices that come into direct or indirect contact with the body, including implants, surgical instruments, and diagnostic tools.
The testing follows internationally recognized standards, such as ISO 10993, which provides a framework for assessing the biological response to medical devices. The process typically involves a series of in vitro (laboratory) and in vivo (animal) tests designed to evaluate the device’s compatibility with the human body. These tests include cytotoxicity (to assess cell damage), sensitization (to check for allergic reactions), irritation or intracutaneous reactivity (to assess local tissue responses), and systemic toxicity (to evaluate the overall effect on the body).
Biocompatibility testing is essential for regulatory approval, as it ensures that medical devices are safe and effective for their intended use, minimising risks to patients and healthcare providers.
The major Biocompatibility standards for medical devices are:
ISO 10993 Series:
ISO 10993-1:2018 – Evaluation and testing within a risk management system
ISO 10993-2:2022 – Animal welfare requirements
ISO 10993-3:2014 – Tests for genotoxicity, carcinogenicity, and reproductive toxicity
ISO 10993-4:2017 – Selection of tests for interactions with blood
ISO 10993-5:2009 – Tests for in vitro cytotoxicity
ISO 10993-6:2016 – Tests for local effects after implantation
ISO 10993-7:2008 – Ethylene oxide sterilisation residuals
ISO 10993-9:2019 – Framework for identification and quantification of potential degradation products
ISO 10993-10:2021 – Tests for skin sensitization
ISO 10993-11:2017 – Tests for systemic toxicity
ISO 10993-12:2021 – Sample preparation and reference materials
ISO 10993-13:2010 – Identification and quantification of degradation products from polymeric medical devices
ISO 10993-14:2001 – Identification and quantification of degradation products from ceramics
ISO 10993-15:2019 – Identification and quantification of degradation products from metals and alloys
ISO 10993-16:2017 – Toxicokinetic study design for degradation products and leachables
ISO 10993-17:2002 – Establishment of allowable limits for leachable substances
ISO 10993-18:2020 – Chemical characterization of medical device materials within a risk management process
ISO 10993-19:2020 – Physico-chemical, morphological, and topographical characterization of materials
ISO 10993-20:2006 – Principles and methods for immunotoxicology testing of medical devices
ISO 10993-22:2017 – Guidance on nanomaterials
ISO 10993-23:2021 – Tests for irritation
ISO 14971:
Medical devices - Application of risk management to medical devices:
This standard emphasises integrating risk management into the design and development of medical devices, including the assessment of biocompatibility risks.
ISO 11135:
Sterilization of health care products - Ethylene oxide - Requirements for the development, validation, and routine control of a sterilization process for medical devices:
Ensures that sterilisation processes used on medical devices do not adversely affect their biocompatibility.
Mechanical and Functional Testing
Mechanical testing evaluates the physical properties of a device, such as its strength, durability, and resistance to wear and tear. Functional testing assesses whether the device performs its intended function under various conditions. For instance, a surgical instrument might undergo testing to ensure it can withstand repeated use without malfunctioning, while a diagnostic device would be tested for its accuracy in delivering results.
Example for medical devices that require this tests:
Implants
Surgical Instruments
Intravascular Devices
Cardiovascular Devices
Prosthetic Devices
Respiratory Devices
Infusion Pumps and Syringes
Wheelchairs and Mobility Aids
Sterilization Equipment
Dialysis Equipment
Patient Monitoring Devices
Dental Devices
Surgical Robots
Sterilization Validation
Sterilization validation ensures that the methods used to sterilise the medical device effectively eliminate all viable microorganisms without compromising the device's integrity. This process involves testing the sterility assurance level (SAL) and assessing the impact of sterilization methods, such as ethylene oxide or gamma irradiation, on the device’s materials. The major standards involving sterilization of medical device / IVD are:
ISO 11135: Sterilization of Health Care Products – Ethylene Oxide – Requirements for the Development, Validation, and Routine Control of a Sterilization Process for Medical Devices
ISO 11137 Series: Sterilization of Health Care Products – Radiation
ISO 17665 Series: Sterilization of Health Care Products – Moist Heat
ISO 14937: Sterilization of Health Care Products – General Requirements for Characterization of a Sterilizing Agent and the Development, Validation, and Routine Control of a Sterilization Process for Medical Devices
ISO 11737 Series: Sterilization of Medical Devices – Microbiological Methods
ISO 18362: Sterilization of Health Care Products – Requirements for Sterilization in Health Care Facilities
ISO 20857: Sterilization of Health Care Products – Dry Heat – Requirements for the Development, Validation, and Routine Control of a Sterilization Process for Medical Devices
ISO 11607 Series: Packaging for Terminally Sterilized Medical Devices
ISO 17664: Processing of Health Care Products – Information to Be Provided by the Medical Device Manufacturer for the Processing of ReSterilizable Medical Devices
ISO 25424: Sterilization of Health Care Products – Low Temperature Steam and Formaldehyde
Electrical Safety and Electromagnetic Compatibility (EMC) Testing
For devices with electrical components, electrical safety testing is conducted to ensure the device operates safely within specified parameters, without causing shocks or malfunctions. EMC testing checks that the device does not interfere with, or is not affected by, other electronic devices in its environment, ensuring it functions correctly without causing or being susceptible to electromagnetic interference.
Example for standards involved:
The IEC 60601/806018 series of standards applies to medical devices and systems that directly apply or transfer energy to the patient, and the IEC 61010-1 standard applies to electrical laboratory equipment. These standards are used in the majority of submissions for electrically-powered medical devices to support device safety. These standards attempt to address all hazards (e.g., mechanical, electrical, radiation). Besides addressing the wide range of generic safety requirements, the IEC 60601/80601 and IEC 61010 series include close to 100 “particular standards” with safety requirements for specific types of devices, such as clinical thermometers, infusion pumps, infant incubators, laboratory centrifuges, medical device sterilisers and reprocessors, and medical washer-disinfectors.
The ISO 14708 Series and ISO 14117 standards assess AIMD when exposed to commonly encountered EM sources as well as particular sources that an implantable device is likely to encounter; along with ISO/TS 10974 Assessment of the safety of magnetic resonance imaging for patients with an active implantable medical device.
IEC 61326-2-6: Electrical Equipment for Measurement, Control, and Laboratory Use – EMC Requirements – Part 2-6: Particular Requirements – In Vitro Diagnostic (IVD) Medical Equipment.
IEC 61000 Series: Electromagnetic Compatibility (EMC).
Sensitivity and Specificity Testing
Sensitivity and specificity tests are crucial for diagnostic devices, particularly those used in detecting diseases or conditions. Sensitivity testing measures a device's ability to correctly identify patients with a condition (true positive rate), ensuring it does not miss cases. Specificity testing, on the other hand, assesses the device's ability to correctly identify patients without the condition (true negative rate), ensuring it does not falsely diagnose healthy individuals. High sensitivity and specificity are critical for the accuracy and reliability of diagnostic tools.
Clinical Evaluation
Clinical evaluation involves testing the medical device in a real-world setting to assess its safety and efficacy in patients. This phase includes clinical trials where the device is used on patients under controlled conditions, and data is collected on its performance, potential side effects, and overall effectiveness. This step is essential for understanding how the device interacts with the human body and ensuring it delivers the intended therapeutic benefits.
Packaging and Shelf-Life Testing
Packaging and shelf-life testing ensure that the medical device remains sterile, functional, and safe throughout its intended shelf life. Tests are conducted to simulate conditions like transportation, storage, and ageing, ensuring the device maintains its integrity and performance until the point of use. This is particularly important for devices with sensitive components or materials that could degrade over time.